After the sensing element produces a presumably desirable output, this signal must be conditioned prior to being analzyed by the oscilloscope, analyzer, recorder or other readout device. As shown in Figure 4, this signal processing can be accomplished by two different methods: (1) internal to the sensor by a microelectronic circuit; or, (2) external to the sensor in a "black box". (PCB uses the registered trademark ICP® to denote sensors which include built-in microelectronics. Sensors without electronics are typically referred to as charge mode sensors.)
Figure 4: Sensor Systems
These analog processing circuits serve the same general functions which include: (1) conversion to a useful, low impedance, voltage signal; (2) signal amplification / attenuation; and (3) filtering. However, it is important to note that the location of the circuit may be critical to the proper operation of the sensing system. A more detailed description of each method follows.
The ICP® sensor will be discussed first. This concept has experienced a large degree of technical improvements since its advancement in 1967. That is, the circuits have become smaller, the component prices have dropped and the signal processing capabilities have increased as a result of miniature integrated circuits and mirco hi-meg resistors. Even with these improvements, the original intent of the idea remains unchanged...simplicity and ease of use. This two-wire system uses a common conductor for power / signal and an additional conductor for the signal ground. The built-in circuits are miniature charge or voltage amplifiers depending on the sensing element type. Power to these components typically comes from an 18 to 30 VDC, 2 mA constant current supply. (Aside from price, convenience and/or features, there is no technical advantage from having a constant current power source which is external or built-in to the readout device.) A detailed system schematic is shown in Figure 5.
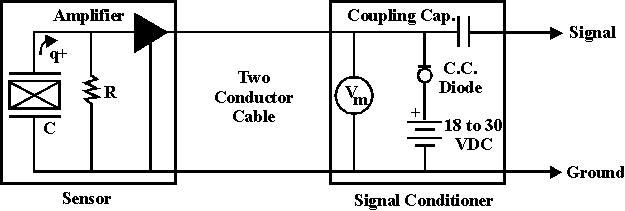
Figure 5: ICP® Sensor System
The characteristics of this system include: (1) built-in microelectronics produce a low impedance, voltage signal compatible with most readout equipment; (2) requires only a simple, easy to use constant current signal conditioner which results in a lower per channel cost; (3) signal is capable of being transmitted over long cables through harsh environments with no loss in signal quality; (4) operating temperature of circuit typically limited to 250 F (121 C) or sometimes 325 F (154 C); (5) functions with ordinary two-conductor coaxial or twisted pair cables; and (6) characteristics of sensor (sensitivity & frequency range) are fixed within the sensor and are independent of supply voltage.
Charge mode sensors utilze the same mechanical sensing structure as do ICP® sensors, however, the signal processing electronics are placed externally. Since integrated, micro-circuits had not yet been developed, the first piezoelectric sensors, which were developed in the 1950's, operated under this principal. These charge systems were often difficult to operate properly and were traditionally expensive as a result of the sophisticated external charge amplifier. (Alternative, lower cost in-line devices are becoming more popular.) Today, charge mode sensors are typically only used in environments where the temperature prohibits the use of sensors with built-in electronics.
As would one might expect, charge mode systems offer various advantages and disadvantages which include: (1) sensor outputs a high impedance signal which requires conditioning prior to being analyzed; (2) requires external signal conditioner (laboratory charge amplifier, in-line source follower, etc...); (3) high impedance signal has the potential to be contaminated by environmental influences such as cable movement, electro-magnetic signals and radio frequency interference; (4) since electronics are external, certain models are capable of operation up to 1000 F (540 C); (5) requires special low-noise cabling; and (6) characteristics of sensor (sensitivity & frequency range) are variable and can be ranged by switching components in the external signal conditioner.