Il DTC è fissato dai componenti dell'amplificatore interno dei sensori ICP. Le specifiche dei sensori di forza ICP riportate in questo catalogo elencano il DTC per ciascun sensore di forza.
Quando si eseguono test con i sensori ICP, per la determinazione delle basse frequenze è necessario considerare due costanti di tempo: una è quella del sensore, che è un valore fisso, e l'altra è quella del circuito elettrico di accoppiamento utilizzato nel condizionatore di segnale.
Quando un sensore ICP è sottoposto a un ingresso a gradini, viene prodotta una quantità di carica, Δq, proporzionale all'ingresso meccanico. Secondo la legge dell'elettrostatica, la tensione di uscita è ΔV = Δq/C dove C è la capacità totale dell'elemento sensibile, dell'amplificatore e del condensatore di misura. Questa tensione viene poi amplificata dall'amplificatore MOSFET per determinare la sensibilità finale del sensore. Dopo l'ingresso iniziale a gradini, il segnale di carica decade secondo l'equazione q = Qe-t/RC dove:
q = carica istantanea (pC)
Q = quantità iniziale di carica (pC)
R = valore della resistenza di polarizzazione (ohm)
C = capacità totale (pF) t = tempo dopo t0
e = base del log naturale (2,71 8)
Questa equazione è anche rappresentata graficamente nella seguente Figura 6:
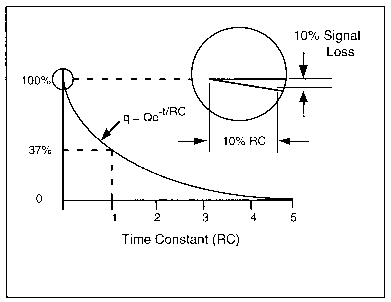
Figura 6: Curva DTC standard
Il prodotto di R e C rappresenta il DTC (in secondi) del sensore. Le costanti di tempo dei sensori variano da pochi secondi a >2000 secondi per i sensori standard. Costanti di tempo speciali possono essere fornite modificando il valore della resistenza, R, nell'amplificatore microelettronico incorporato del sensore.
La maggior parte degli strumenti di lettura ha un'alta impedenza di ingresso, >1 Megohm. Per questi sistemi, il DTC del sensore, come discusso in precedenza, diventa il valore dominante e può essere utilizzato per determinare la velocità di scarica del segnale. Tuttavia, per i segnali accoppiati a dispositivi di lettura a bassa impedenza, generalmente <1 Megohm, è necessario determinare la costante di tempo del sistema. Questo aspetto verrà spiegato ulteriormente nella sezione seguente.